Porosity in Welding: Identifying Common Issues and Implementing Best Practices for Avoidance
Porosity in welding is a pervasive concern that usually goes undetected up until it causes significant troubles with the stability of welds. This common defect can endanger the stamina and sturdiness of welded frameworks, presenting security risks and bring about pricey rework. By comprehending the origin of porosity and executing reliable prevention strategies, welders can dramatically enhance the quality and integrity of their welds. In this discussion, we will certainly explore the vital aspects contributing to porosity development, examine its destructive effects on weld efficiency, and talk about the very best methods that can be taken on to lessen porosity occurrence in welding processes.
Common Reasons For Porosity
An additional constant culprit behind porosity is the presence of contaminants externally of the base metal, such as oil, grease, or rust. When these impurities are not effectively removed before welding, they can evaporate and come to be caught in the weld, creating issues. Additionally, utilizing filthy or wet filler materials can present pollutants right into the weld, adding to porosity issues. To reduce these typical reasons of porosity, thorough cleansing of base steels, appropriate shielding gas option, and adherence to ideal welding specifications are important practices in attaining top notch, porosity-free welds.
Influence of Porosity on Weld High Quality

The presence of porosity in welding can substantially endanger the structural stability and mechanical buildings of welded joints. Porosity produces spaces within the weld steel, damaging its general toughness and load-bearing capability.
Welds with high porosity levels tend to show reduced effect stamina and decreased ability to deform plastically prior to fracturing. Porosity can hinder the weld's capability to successfully transfer pressures, leading to early weld failure and potential safety and security dangers in vital structures.
Best Practices for Porosity Avoidance
To enhance the structural stability and top quality of bonded joints, what specific steps can be carried out to decrease the occurrence of porosity during the welding process? Utilizing the right welding strategy official source for the details product being welded, such as changing the welding angle and gun setting, can additionally protect against porosity. Normal inspection of welds and immediate remediation of any issues determined throughout the welding process are essential practices to avoid porosity and create premium welds.
Value of Appropriate Welding Methods
Carrying out appropriate welding check out here methods is critical in making sure the architectural stability and quality of welded joints, building on the foundation of reliable porosity avoidance procedures. Welding methods directly impact the total toughness and toughness of the bonded structure. One key facet of correct welding methods is maintaining the correct warmth input. Too much warm can lead to increased porosity as a result of the entrapment of gases in the weld swimming pool. Conversely, insufficient warmth may result in insufficient combination, creating possible weak factors in the joint. Additionally, making use of the proper welding parameters, such as voltage, existing, and take a trip speed, is critical for attaining audio welds with marginal porosity.
In addition, the choice of welding process, whether it be MIG, TIG, or stick welding, should line up with the specific requirements of the task to ensure ideal outcomes. Correct cleaning and preparation of the base steel, along with selecting the best filler product, are also vital parts of competent welding techniques. By adhering to these ideal practices, welders can decrease the risk of porosity formation and create high-quality, structurally sound welds.
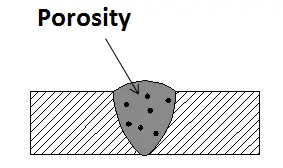
Checking and Top Quality Control Steps
Examining treatments are crucial to detect and prevent porosity in welding, ensuring the toughness and durability of the last item. Non-destructive screening techniques such as ultrasonic testing, radiographic testing, and aesthetic examination are generally utilized to determine potential issues like porosity.
Performing pre-weld and post-weld assessments is also essential in preserving quality assurance criteria. Pre-weld assessments involve validating the materials, tools settings, and cleanliness of the job area to avoid contamination. Post-weld examinations, on the other hand, assess the final weld for any kind of flaws, consisting of porosity, and verify that it meets specified criteria. Executing a comprehensive quality assurance strategy that includes detailed testing treatments and evaluations is extremely important to decreasing porosity concerns and ensuring the general top quality of welded joints.
Conclusion
To conclude, porosity in welding can be a typical concern that influences the quality of welds. By identifying the typical reasons for porosity and carrying out best techniques for avoidance, such as correct welding strategies and screening measures, welders can ensure excellent quality and reputable welds. It is necessary to prioritize avoidance techniques to lessen the occurrence of porosity and review maintain the integrity of welded structures.